How Bottle Unscrambling Machines Enhance Quality Control in Production
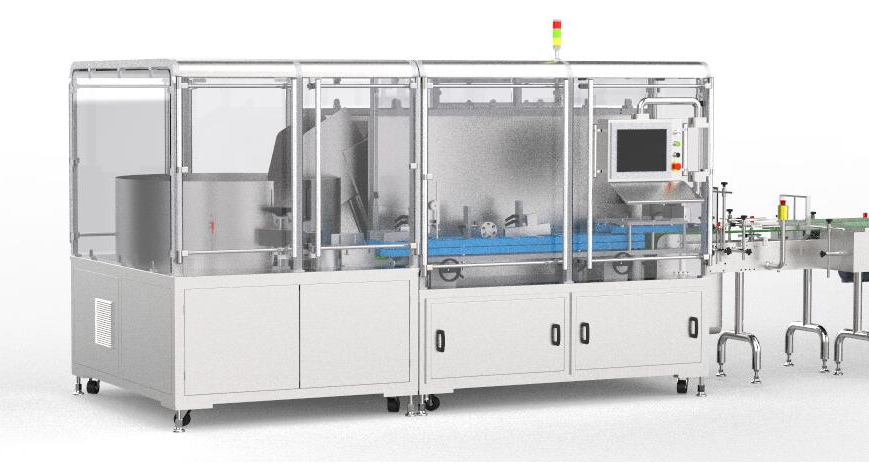
In the environment that manufacturing and packaging processes take place, timely management of quality is critical. In industries that use bottles in their products, it is essential to get the bottles right for filling through proper orientation. This is where the bottle unscrambling machine will be of assistance. These are used in order to improve speed of sorting and orienting bottles and as well improve the quality of the product within the production line. This is how first in first out or the bottle unscrambling machines can help ensure that the quality management remains high in manufacturing.
Streamlined Bottling Process
Bottle unscrambling machines play a major role in the depone mechanism of the bottling system. They effectively organize and position lots of bottles fast while always making minimal mistakes. To employ this, manufacturers are capable of minimizing human error and that explain the frequent cause of quality problems. In the case where bottles situated are dislocated or possibly sited in the wrong manner, it results to filling difficulties and sometimes spills and other manufacturing defects. An unscrambling machine helps in making certain that every bottle is rightly oriented before it gets to the filling area, thus increasing product standardization in production.
Improved Filling Accuracy
Accuracy in filling is important to ensure that the product quality and that it meets the mandatory standards in the sector. An unscrambling of bottles for example aids in increasing the accuracy because each bottle will be in the right position to be filled. This method allows the forming tips to pour a precise amount of liquid as well as to fill each of the bottles to the required level. This precision does not only improve the quality of the product but also eliminate the possibility of a product recall or penalties for violation of regulatory requirement.
Low Labour Expenses Cutting and Efficient as Compared
There are also cost savings that will be achieved since the process of unscrambling the bottles will be fully automated while positions of bottles will also have to be moved by human beings which might be an added expense. This automation is the reason that the organization’s employees can dedicate time and energy to more productive matters including supervising the production line and checking quality. However, the good results obtained from a bottle unscrambling machine allow for the throughput capacity of the line to be increased, thus allowing for more bottles to be sorted in the same amount of time. Such efficiency implies that the possibilities for a more efficient manufacturing process are greatly enhanced, as is quality assurance.
Enhanced Product Integrity
Bottles including the glass and plastic ones can easily break down during handling and moving. Self-decoding often means improper handling of the product and this leaves some of the bottles broken at the neck or cracked. An unscrambling machine specific to bottles ensures that bottles are treated with an utmost care in order to avoid accidents especially while sorting them. The shape, size and structure of bottles protect their content from adverse effects of external environment during the period from production of the product to its delivery to the consumer, thus preserving the image of the brand and consumers’ trust.
Real Time Tracking and Data Gathering
Most of today’s unscrambling machines include some high-tech features that help monitor the process of bottling in real time. These machines can record KPIs things like the speed of sorting, the level of errors committed and the performance of the machines being used. The following information facilitates reaching the goal of detecting sources of potential quality control problems before they emerge. This approach of process analysis will also enable the companies to make adequate decisions on processes such as improvements and preventive measures, all of which will add to a noble level of quality control.
Flexibility and Adaptability
In the current setting for manufacturing, one of the critical success factors is flexibility. Another benefit brought about by using the bottle unscrambling machines is its ability to accommodate different sizes and shapes of bottles in a single line hence flexible for usage when the production scales change. Manufacturers are therefore able to adjust production conveniently in accordance to market needs or changes in product portfolio without adversely affecting product quality. Majidkhah & Tavakoli, 2010, have suggested that a suitable unscrambler can adapt to a new bottle design or a new product line appropriately.
Conclusion
Introducing a new bottle unscrambling machine in the production line is a tactical decision for manufacturers willing to improve the quality. It also upgrades the filling of the bottles to allow more precise servings, while also cutting down the number of workers needed and coming with the benefits of conserving the integrity of the product. They are a very sophisticated solution as they can monitor quality in real time and can also be applied to different types of bottles. Based on the growing trend of sales of quality bottled products, manufacturers cannot afford to be associated with rudimentary technologies such as the conventional systems used to unscramble bottles among several others and, therefore, need to consider applying innovative technologies on the market as the bottle unscrambling machines.